Australian scientists have published an 'instruction manual' that makes it a whole lot easier and cheaper to create metallic glass - a type of flexible but ultra-tough alloy that's been described as "the most significant materials science innovation since plastic". The material is similar to the sci-fi liquid-type metal used to create the T-1000 in Terminator 2 - when it's heated it's as malleable as chewing gum, but when it cools it's three times stronger than steel.
Researchers have been dabbling with the creation of metallic glass - or amorphous metal - for decades, and have made a range of different types by mixing metals such as magnesium, palladium, or copper - but only after an expensive and lengthy process of trial and error. Now, for the first time, Australian scientists have created a model of the atomic structure of metallic glass, and it will allow scientists to quickly and easily predict which metal combinations can form the unique material.
"Until now, discovering alloy compositions that form these materials has required a lengthy process of trial and error in the laboratory," lead researcher Kevin Laws from the University of New South Wales (UNSW) said in a press release. "With our new instruction manual we can start to create many new useful metallic glass-types and begin to understand the atomic fundamentals behind their exceptional properties."
The difference between metallic glasses and regular metals is their atomic structure. Normal metals are crystalline when solid, which means their atoms are arranged in a highly organised way. Metallic glass alloys, on the other hand, have a highly disordered structure, with their atoms arranged irregularly.
The new model, which is described in Nature Communications, looks at the atomic structure of different metals and identifies whether they'd be able to create a metallic glass. Using this model, the UNSW researchers have already successfully predicted more than 200 new metallic glass alloys based on magnesium, silver, copper, zinc, and titanium.
"We will also be able to engineer these materials on an atomic scale so they have the specific properties we want," said Laws.
The biggest benefit of this model isn't necessarily to researchers - although it will make their lives a lot easier. What's really exciting about it is that it might finally make the bulk production of these awesome materials commercially viable.
"Metallic glass alloys are expensive to manufacture and to date have only been used in niche products, such as ejector pins for iPhones, watch springs for expensive hand-wound watches, trial medical implants, and tennis racquets and golf clubs. They are also planned for use in the next Mars rover vehicle," said Laws.
"But if they become easier and cheaper to make, they could be widely used in many applications, including as exceptionally strong components in personal electronic devices, in space exploration vehicles, and as hydrogen storage materials in next generation batteries," he added.
Last year, scientists used metallic glass to create an iPhone case that was 50 times harder than plastic. You can see the process in action below:
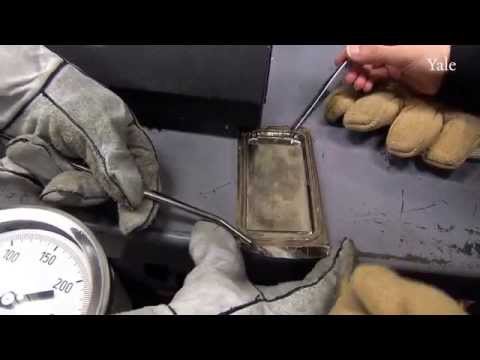
That's cool enough, but it's only the beginning. If we can make the manufacturing process cheaper, we'll see a whole range of these types of innovations hitting the market in the years to come - imagine the back of your iPhone being made out of metallic glass instead of just a case. Or cars made from the material.
Because, let's face it, plastic is great and all, but we could all use a little more durability in our lives.
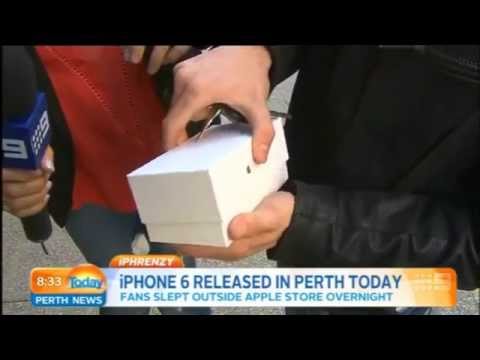
Love science? Find out more about the groundbreaking research happening at UNSW Science.